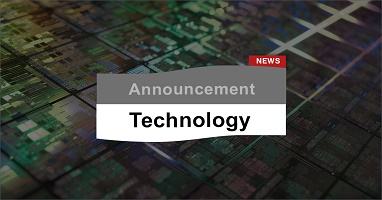
Progress moves technology closer to availability of a standard foundry process designed to greatly increase compute performance and energy efficiency
BLOOMINGTON, MN, July 25, 2019 – SkyWater Technology Foundry, the trusted innovation partner for tomorrow’s most advanced technology solutions, and Massachusetts Institute of Technology (MIT), announced an update at the 2019 ERI Summit on the DARPA sponsored 3DSoC program, the largest of the ERI programs. The program is being led by MIT and supported by Stanford University and SkyWater; the team has achieved progress in transferring the carbon nanotube (CNT) Field Effect Transistors (FET)-based 3DSoC technology into SkyWater’s 200mm production facility after years of development work and successful concept demonstration at MIT. The benefits of such breakthrough technology will set a new benchmark for compute performance and energy efficiency and is a pivotal move towards bringing back cutting-edge manufacturing to the U.S.
The technology supports monolithic integration of stackable tiers of CNT-based logic and RRAM to realize a high-density SoC architecture. To fabricate the 3DSoC, SkyWater is using a 90nm process which is predicted to deliver power/compute performance exceeding that of conventional 2D architectures fabricated with 7nm process flows. Though this demonstration is using 90nm geometry, the technology is compatible with node scaling for further performance gains. While observers note the program’s ambitious objectives and potential challenges, the initiative is tracking to plan as the first year concludes.
To date, the new SkyTech Center has been commissioned within SkyWater, which includes all the capital equipment required to support the program. Unit process steps as well as a complete process flow from MIT have been transferred successfully to SkyWater’s 200mm processing facility and the program is currently running a wide variety of test chips to continue to jointly develop the technology and demonstrate its potential.
“I am thrilled to see the progress and many steps taken on this road in transitioning our work from our academic lab at MIT into the real world through SkyWater’s volume manufacturing facility,” said Dr. Max Shulaker, MIT Professor of Electrical Engineering and Computer Science. “The close collaboration between MIT, Stanford, and SkyWater has proved critical in progressing these nanotechnologies toward widespread adoption.”
“SkyWater has been focused on breaking the mold of Moore’s Law scaling from our start. This technology holds great promise for doing exactly that, by not only putting the industry on a new compute/performance scaling path, but by shining light on new paths to enable the next wave of artificial intelligence and machine learning,” said Dr. Brad Ferguson, SkyWater Chief Technology Officer. “Max and the team at MIT are making an enormous contribution to the industry and we greatly value the opportunity to play a role in bringing this new IC architecture to market.”
About SkyWater Technology Foundry
SkyWater is a solely U.S.-based and owned, DMEA-accredited Technology Foundry, providing custom design and development services, exclusive design IP, and volume manufacturing for integrated circuits and micro devices. The Company’s world-class operations and unique processing capabilities enable mixed-signal CMOS, rad-hard and ROIC solutions. SkyWater’s Innovation Engineering Services empower development of superconducting and 3D ICs, along with carbon nanotube, photonic and MEMS devices. SkyWater serves customers in growing markets such as aerospace & defense, automotive, cloud & computing, consumer, industrial, IoT and medical. For more information, please visit: www.skywatertechnology.com/.
SkyWater Company Contact: Ross Miller | 952.851.5063 | ross.miller@skywatertechnology.com
SkyWater Media Contact: Lauri Julian | 949.280.5602 | lauri.julian@skywatertechnology.com